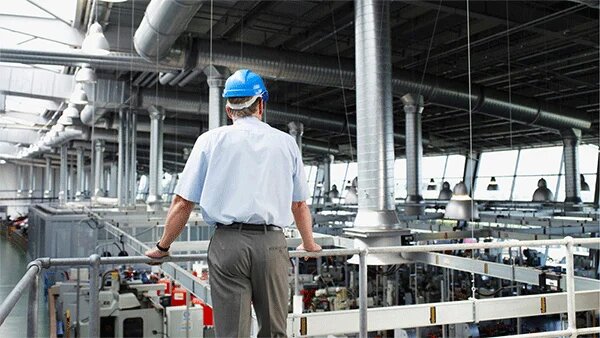
Why Lean Manufacturing Needs Data Integration
In the pursuit of waste reduction and quality maintenance, dynamic processes are paramount. The integration of data systems, spanning from internal operations to collaborative partnerships, plays a pivotal role in achieving data-driven lean manufacturing, fostering real-time decision-making and enhancing overall productivity.
Originating in Japan in the 1950s, lean manufacturing has evolved into a dynamic approach focused on minimizing waste across various dimensions such as material, work resources, and time. At its core, lean manufacturing aligns closely with just-in-time production (JIT), emphasizing the production of the right product, in the right quantity and at the right time.
JIT encompasses three key processes:
-
Continuous flow: streamlining the production process to optimize quality and storage space, and to increase the availability of ready-to-ship products.
-
Takt time: synchronizing production rates with customer demand to ensure efficiency and responsiveness.
-
Pull system: controlling production based on actual customer demand to avoid excess inventory and overproduction.
To achieve waste reduction and meet customer demands while maintaining high-quality standards, dynamic processes are crucial. This is where data becomes pivotal.
The integration of data systems, both within the company and in collaboration with suppliers and customers, is essential. The progression towards data-driven lean manufacturing and JIT production involves three key maturity steps:
-
System integration: establish a comprehensive connection between data sources within your company, including suppliers, internal processes, assets, and customer information.
-
Data utilization: automatically and proactively leverage the connected data to optimize workflows, enhancing overall operational efficiency.
-
Forecasting and collaboration: utilize streamed data to refine planning processes, forecast business needs, and foster improved collaboration and partnerships.
In the realm of lean manufacturing, strategic data integration is instrumental. It facilitates real-time decision-making, reduces operational inefficiencies, and enhances overall productivity. With seamless connectivity across the supply chain—from suppliers to internal processes and customers—manufacturers can unlock the full potential of lean principles.
By integrating data systems, manufacturers gain a holistic view of their operations. This visibility enables them to identify areas for improvement, minimize bottlenecks, and enhance overall production efficiency. The continuous flow, takt time, and pull system are not isolated components but interlinked elements of a streamlined manufacturing process powered by data insights.
Embarking on this journey requires a strategic approach. For a useful starting point or guide for those already on the lean manufacturing path, make sure to check out how we’ve helped our customers in the past.